Optimisation of the Manufacture of Inconel 718 Parts.
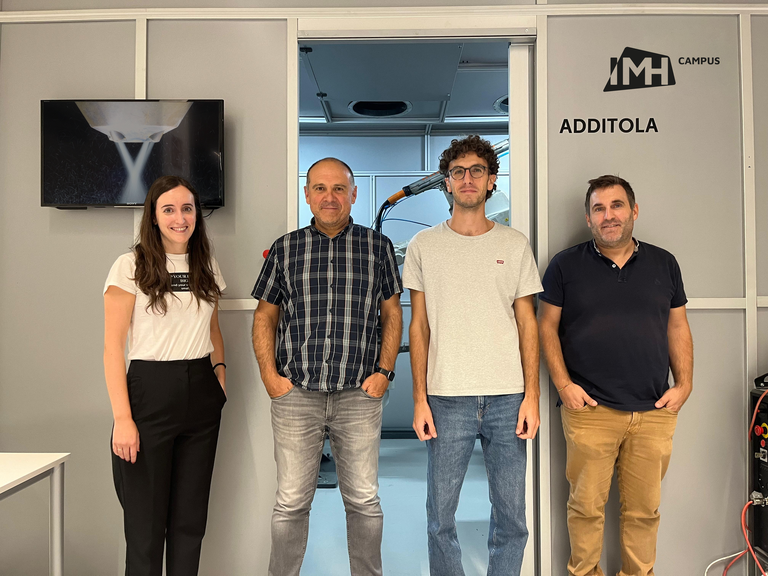
A team of researchers from the Department of Additive Manufacturing at IMH Campus is carrying out a pioneering study on the optimisation and statistical modelling of the manufacturing process of Inconel 718 parts using Direct Metal Deposition (DMD) technology. This work, recently published, aims to analyse how different process parameters, such as laser power, feed rate and powder flow, affect the geometry and properties of the manufactured parts through the use of statistical tools.
Three-Phase Methodology
The study is carried out in three distinct phases:
Phase 1: Optimisation of parameters for single bead deposition.
Phase 2: Optimisation of parameters for the deposition of monolayer coatings.
Phase 3: Optimisation of parameters for the manufacture of three-dimensional (3D) parts.
The team finds that the three input parameters (laser power, powder flow and feed rate) have a significant impact on the characteristics of the individual beads, which correspond to the aspect ratio, contact angle and dilution ratio. Furthermore, they determine that the percentage of overlap between beads is crucial for reducing the standard deviation of coating height and surface porosity in single-layer coatings. In terms of 3D part manufacturing, it is found that the programmed layer height directly influences the height error of the parts, and this parameter is optimised to minimise such errors.
In conclusion, the research demonstrates that the statistical methodology employed is effective in optimising the process parameters at each stage, resulting in a significant improvement in the quality of the manufactured parts.
This study reinforces IMH Campus as a benchmark in applied research in Additive Manufacturing and highlights the team's commitment to innovation and excellence in the industrial sector.